I've learned a lot from the DIY type shows on TV. There's one power tool all the guys use that just gets the job the heck done. I've had the pleasure to sample and to master it on my own projects. Of course, it's
stubble. The ole' five o'clock shadow isn’t quite enough to pull it off; you need a professional-grade semi-beard to achieve success in today's demanding renovation projects.
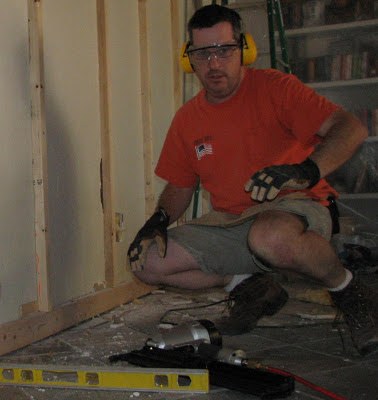 |
AZ DIY Guy with full stubble & kung-fu action grip |
I support my claim with first-hand experience. Over many trials, I have broken my weekend projects into meaningful data. Then it's a simple analysis of mathematics and production. I have found that I complete 80% of my weekend projects on Sunday,
with a healthy two-day stubble. Normally, by Saturday, I'm only halfway through my planned weekend projects, naturally due to the mere overnight dusting of a single-day's chin whiskery on my mug. Coincidence? I think not. Conversely, if I had to appear somewhere on Saturday as a clean-shaven gentleman about town, my weekend projects tended to suffer, when starting fresh on Sunday. It's almost as if I lost a day's work, just because I am elsewhere half the time,
in a semi-smooth faced condition.
Features
Stubble actually enhances the brain's neurological problem-solving center. Men are subconsciously trained from birth that a good scratch of the stubble* sends a blast of mental adrenalin to quickly devise an appropriate solution. This knowledge is reason that generations of cartoons have portrayed countless legions of idiots and feeble-minded morons as fools, scratching the top of their heads. They are so stupid that they are scratching the completely wrong side of their head!
Wouldn't you prefer to see your hired electrician silently rubbing his stubbled chin, as he assesses the complexities of your electrical service panel, using his knowing, steely gaze, rather than a smooth-chinned, slack-jawed yokel, scratching his unkempt hair, poking at the panel, glassy-eyed, with a bent twig, "duuuuuuuhhhh...."?
* A proper stubble scratch should be performed with a loose fist-like gesture, palm downward with a good, slow thumb and index finger stroking motion. Additionally, at no time should a single-sided, multi-finger rapid scratch be used. It just looks like a hound trying to dislodge a chigger, and is clearly beneath the status of any true tool-wielding craftsman.
Confidence.
Do you really think you can handle an 18 volt reciprocating-saw, with a heavy demolition blade, while perched smooth-faced and daintily on your eggshell-white step stool, in your khaki Dockers and a Polo shirt? Or are you going to get your grizzle-jawed self up a 8 foot, class III ladder in your Carhartt's and rip through a nail encrusted wall in a shower of sparks, drywall, and burning sawdust? Damn right you are!
Confidence man!
The Research.
You don't have to trust my experience. Again, look to the cable TV renovation expert dudes. Nine times out of ten, they're sporting a good, perfectly-maintained stubble. Would the homeowners even trust them to touch their home otherwise?
There's that
Property Brothers show where the twin brothers find and fix up a house for a young couple that can't afford to buy what they want outright. One is smooth-ish faced, the other measurably scruffier. Can you guess which one is the realtor and which one knows how to sledgehammer out a non-load bearing wall and create a high-end commercial kitchen out of a musty coat closet full of dead mice?
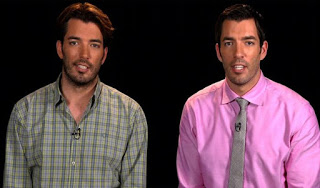 |
Pop Quiz: Which one is the Realtor and which one can jackhammer the floor out of a basement?
Hint: Compare the area between their ears and their collars. |
The real rock stars of the craft sport old school, full-time facial trophies. I'm talking about Tom Silva, Roger Cook, and Norm Abrams of
This Old House. Heck, they don't even comb their hair on the jobsite, they're too busy kicking old house ass with their full beard and / or moustache. But this is about what an everyman can accomplish, not a deity of the construction realms.
Even fictional Hollywood handymen follow the rule. Why do you think clean shaven Tim "The Tool Man" Taylor's projects so rapidly imploded into chaos, while the Al Borland shook his head knowingly, luxuriating in his Bob Vila beard?
The only guys that can pull off a smooth face reno without being laughed off the project seem to have decided to go spear bald. I haven't figured it out yet, but the chrome dome look seems to share some of the same powers as the stubble. I'm not yet willing to do any personal experimentation on this aspect.
I further recognize that the cadre of female cable TV fix-it-up experts don't go the facial stubble route, but they seem to finish their work admirably well regardless. I can only surmise by the evidence I can gather from my observations that this is accomplished through one of two methods.
- The use of tousle-haired meathead sidekick carpenter that seems to change every few episodes. These guys are each outfitted complete with stubble, an empty leather tool belt, nail guns and a sliding-compound miter saw.
- The too-tight, V-neck lady T-shirt. You know, the one with the weirdly too short sleeves. I don't understand the science, but there seems to some commonality to their garb on these shows. I suspect that it is the female version of man-stubble and should be attributed the same way to their success. They can't reasonably pull off a successful chin-scratch power move, but there seems to be a maneuver involving the position of the camera in relation to a quick hint of cleavage whilst circular sawing or shooting a nail gun. I truly think it's the tasteful use of boob-age that does the trick. I haven't put it to the test myself because I simply get good results by letting my facial hair grow out a couple days; I don't see the need to work dressed in a too-tight, V-neck lady T-shirt, plus I look terrible in pastels.
Value.
The stubble, employed properly is one of the most economical additions you can use in your shop or work site. The cost is not too overly bad and compares very favorably against power tools equipped with laser targeting. The cost consist of:
- The pain of carving it off your face Monday morning as well as the price of blades.
- The uninitiated simply don't realize the toll stubble takes on your wardrobe. The 60 grit sandpaper on your neck tears the heck out of the collar of an otherwise serviceable flannel work shirt.
- The degraded feeling you get when you see that baby-smooth chin in the mirror, your cheeks flush with razor burn and your fresh shaven whiskers laying in the sink, their power ebbing back to the cosmos.
An added value is the pure entertainment and quality time you can have with your kids each week as you purposefully and creatively shave ever larger amounts off and pause to pose for their momentary admiration. One can share the enjoyment of the various forms of the goatee, pork-chop sideburns, and the handlebar mustache before moving to the ever-popular "molester" pencil moustache, the "Hitler" tooth-brush looking thingy under your nose, or whatever various artistic free-form oddities your mind can create.
Caution: For some unknown reason, wives don't seem to appreciate this benefit. Why an eye roll is necessary when their loving husband struts around the house for a few minutes with a good ole' Hitler mustache, I just don't know.
I believe the addition of good quality man stubble to your toolbox will improve your work quality and productivity. Give it a try. If all you can pull off is a peach fuzz, or a mangy cat look , perhaps try the chrome dome or the too tight, V-neck lady T-shirt method.
Then again, there is an exception to every rule.
<UPDATE> Stop the presses! This manly, manly post won the coveted "Manliest link up so far to Man Up Link Up." award over at So I Married A Craft Blogger. Check his site out, a Man's view of the world of craft blogging.